Blog Article
Beyond the Assembly Line: Quality Controls within the Manufacturing Industry
No matter industry or company, every manufacturing company is connected through one thing: the unwavering commitment to quality control. It forms the foundation for every manufacturing process and gives stakeholders and clients the trust and confidence they need so that they can hold continuous loyalty to companies. But what other major significance does it hold within this industry? Let’s dive in and explore the far-reaching impact quality controls have on manufacturing companies.
Firstly, what is quality control? Quality control is the systematic process that aims to guarantee the consistency and excellence of products. It monitors every stage of the manufacturing journey, from product idea through to final sale, it’s in place to ensure that everything that leaves the production line is up to the highest standard and is a testament to precision.
At its core, quality control optimises operational efficiency. By identifying potential flaws early on in the manufacturing process, it reduces the chances of costly reworks and delays in production. Translated, this means companies are working on streamlined production cycles, reducing waste and ultimately increasing productivity. All benefits craved by companies in this industry.
However, where there is excellence, there is expectation. Customer / client satisfaction is the key to success, and with reviews that can tear down reputations in singular seconds, having a good quality control strategy is crucial. Not only does it aid in gaining customer / client trust, but it ensures that products not only meet expectations, but surpasses them. A happy customer / client is the aim of the game, and so quality control processes help loyalty flourish, as no one loves anything more than products that consistently perform as promised.
Consistency is the foundation for a sterling reputation, and a company’s reputation is it’s most treasured asset. One negative review will outshine a thousand good ones, so regular consistency is one of the most important things. By implementing quality controls, companies can build a reputation on excellent service, outstanding quality and a high standard of customer / client care.
In essence, quality control is the centre of manufacturing success, which is why you find so many companies within the industry, holding various ISO (International Organisation for Standardisation) standards. Whilst for some, ISO is a prerequisite for winning business, it isn’t the same for all. However, whether you planned to be certified or not, quality processes are key to long term success, so why don’t you start investing?
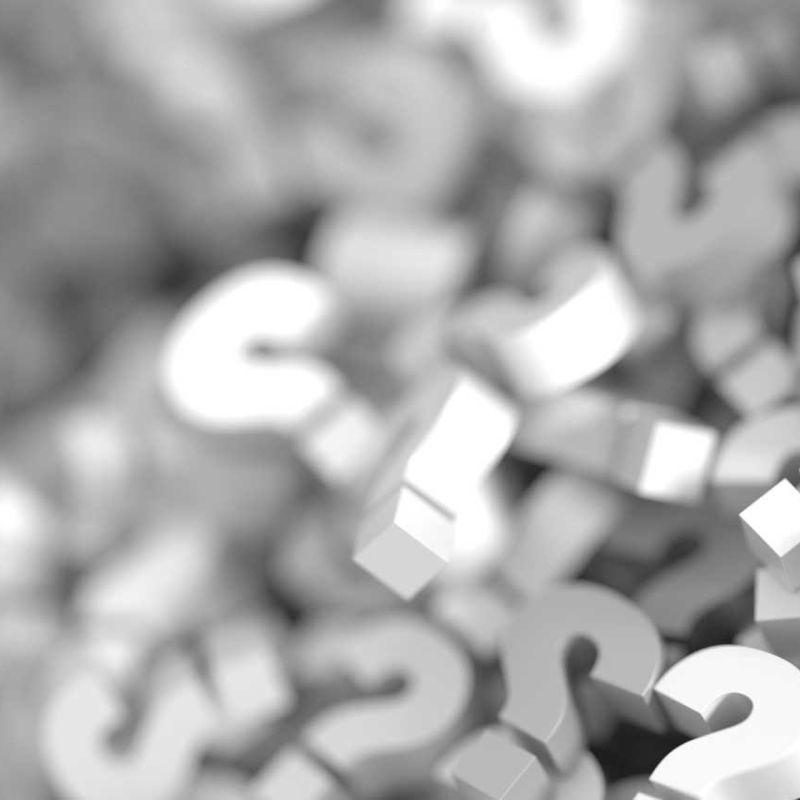